In this blog, I'm sharing the great knowledge-enhancing experience of the Welding Training provided by Mr.Ashok Bezalwar at Advent.
Advent conducted training sessions for the welding team members by welding expertise to enhance & grow up the skill of welders & update welding knowledge.
The training was very helpful to ensure what skills are necessary to successfully enter into this field. This training was completed in two sessions with lectures & practical exercises. During training, he started from welding fundamentals which is necessary for welders.
He explained that a welder should have certain skills before starting welding, including knowledge of geometry & trigonometry for measuring angles, types of forming joints, and calculating the correct length, welding drawing readings for example, welding symbols, types etc. Besides this he/she needs to understand the properties of different types of materials too. He also gave practical training to welders about what welding parameters to keep during welding process, how to handle the welding gun considering all the safety precautions.
1. Welding Basic
The training started from the basic introduction of welding that is, what welding is & its applications, everything about correct power voltages, metals and consumables. Welding is the process of joining the two materials by fusing them using heat energy, Pressure or both & concentrated along with seams. The basic purpose of welding is to join two elements together with a firm connection.
Welding is used to create many modern constructions in our world, such as automobile industries, skyscrapers, cars, ships and airplanes etc. The parts that are joined together are known as base materials. The material that is added to form the joint is called a filler material or consumable.
2. Welding Process
The number of different welding processes has grown up in recent years. These processes differ in the manner in which heat & pressure are applied & the type of equipment used. Which welding process is applicable depends on the types of materials, dimensions, thickness, size & shape, available welding position, joint preparations, available power source, quality levels & economics etc.
Different job required different types of welds. TIG (Tungsten Inert Gas) & MIG (Metal Inert Gas) welding are preferred in automobile parts assembly where the weld has to have a fine & polished appearance.
3. Types Of welding Joints
There are five basic types of welding which are commonly used in manufacturing. These are:
4. Importance of welding Symbols :
Welding symbols play a vital role in the welding process. Clearly marked welding symbols give clear information to the welders of what to place where, size of the weld & what kind of weld is to be applied to achieve best weld quality. So, it is very important that the designer also should clearly mark welding symbols in 2D welding drawing.
Welding symbols convey the very complicated instruction in very simple format to the welders. Also it helps to ensure the consistent quality & tolerances required for the welding assembly.
5. Welding Defects
Most defects encountered in welding are due to an improper welding procedure. Once the causes are determined, the operator can easily correct the problem.
- Lack of Penetration or Incomplete Penetration.
- Lack of Fusion or Incomplete Fusion.
- Undercut.
- Spatter.
- Slag Inclusions.
- Cracks.
- Porosity.
- Overlap.
6. Safety Consideration during welding-
Welder safety is very important because it can be a very dangerous workplace activity which may causes hazardous situation or accidents. Therefore, it is very important that welders must be aware about the welding risks & potential hazardous situations. During welding, one should follow the safety rules & use PPE for:
- Eye Protection
- Eye & Face Protection
- Heat & Radiation Protection
- Electrical shock protection
- Fire Protection
- Foot & Hand Protection
7. Welding Inspection & Quality Control
After welding is done, one important and necessary role is to inspect the quality of the weld for ensure satisfactory performance. There are different welding inspection methods being used.
During welding inspection many parameters are to be checked, including weld size & welding defects. Weld size is a very important parameter because it is directly related to the weld strength & performance of the weld. In automobile part assembly, welding size & location of weld is very important.
Welding discontinuities are referred to as welding defects which may cause premature weld failure due to stress concentration & strength reduction in welded components. The welding inspector must have prior knowledge of welding procedures, inspection methods like Visual inspection, Destructive & Non-destructive Testing, fabrication drawing readings, welding symbols, weld joints design, weld standard requirements & acceptance criteria. Also, he/she should be aware about the properties of the material(s) being used for welding.
Methods Of Welding Inspection –
1 . Visual Inspection
Visual weld inspection is the one of the easiest methods for inspection. In visual inspection, one can check the welding defects like cracks, pits, porosity, undercuts, missed joints in weld etc. visually. It also involves the checking of weld size and weld location as per requirements.
2. Non-Destructive Testing (NDT)
There are two most commonly used NDT methods - Dye Penetrate Testing & Magnetic Particle Testing. By using these methods, weld cracks & other discontinuities can be easily found out.
3. Destructive testing (DT)
This inspection method involves physical destruction of the weld to detect various mechanical & physical properties of the weld.

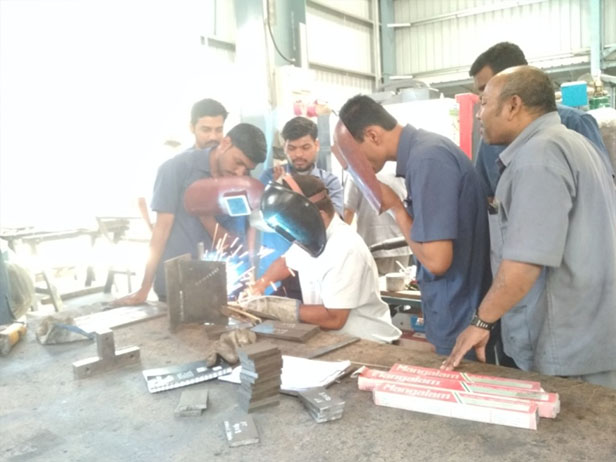
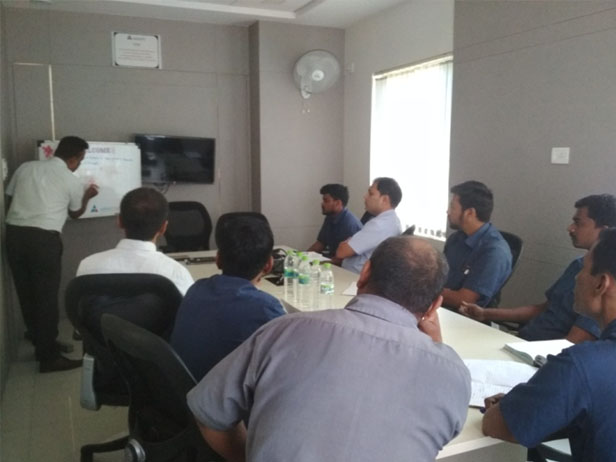
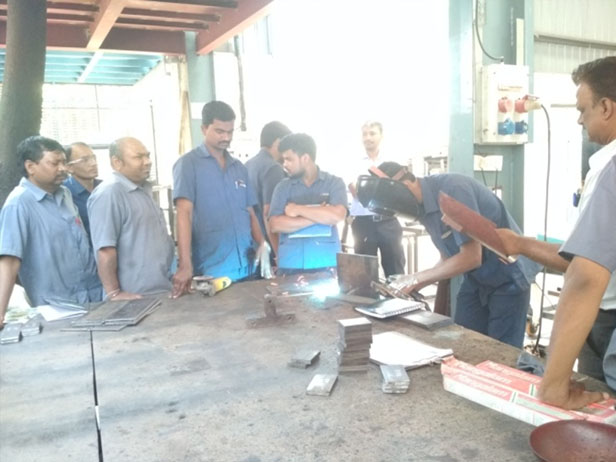
Leave a Reply