Finding the perfect solution to a tough fabrication challenge takes a serious amount of skill, invention, and creativity. And it’s within these moments of challenge that our team gains the most.
At Advent, Welding & fabrications involves the process of designing metal structures & as per design building the metal structures for checking fixtures, special purpose machine(SPM) throughout the weld. Also we export weldings of Tool assemblies, Automotive part assemblies, Aerospace parts assemblies.
THE CHALLENGES & REQUIREMENTS FROM THE CLIENTS:
- Welding required as per standard and dimensionally accurate as given in drawings.
- Welding Inspection report & Non-Destructive Testing(NDT) reports.
- Qualified & Certified welders.
- No cracks or holes, pits, undercuts & surface cracks in the welding bead.
- The bead must have uniform waves, width and height.
- The finished product must satisfy the design dimensions and has almost no distortion.
- The welding must meet the required strength.
THE PROBLEMS & SOLUTIONS:
SOLUTION FOR “I-STAND” WELDING DISTORTION
Problem 1
Initially, During welding of I-stand, we found distortion in the parallelism of two resting planes or faces i.e. two resting pads because of many factors like Improper tube cutting, less holding force during welding.
Advent Solution
- Whenever we used to manufacture & weld the I-stand we found distortion & bending problems in resting pads. To solve these problems we found out a solution that is, we manufactured a welding jig for holding the I-stand with the parallel resting plane properly.
- We made adjustable welding jigs to weld the different lengths of I-stands. (As shown in image)
- We standardized this template for Welding process.
Benefits
- With the help of this I-stand welding jig welding lead time is reduced.
- Resting pads are easily hold in 90 degree to weld.
- Resting pad distortion & bending problem completely solved.
- No need of extra man power to hold the resting pads during welding.
- Time consumable.
- Reduced tact time for further drilling process by using this welding jig.
- Differ lengths of I-stands can easily weld with this adjustable welding jig.
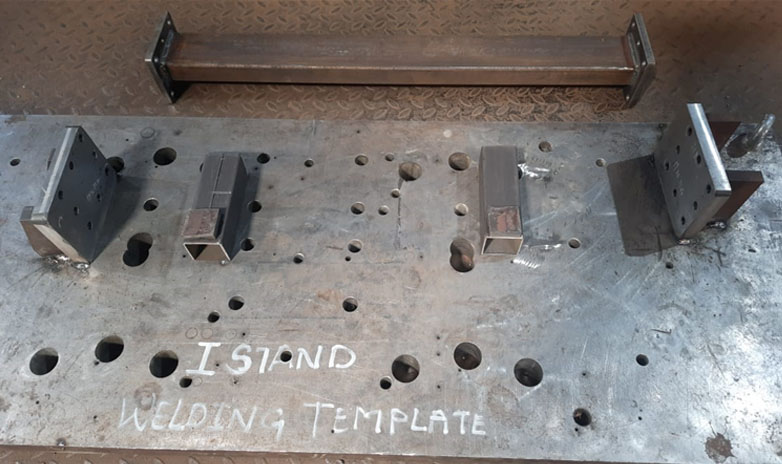
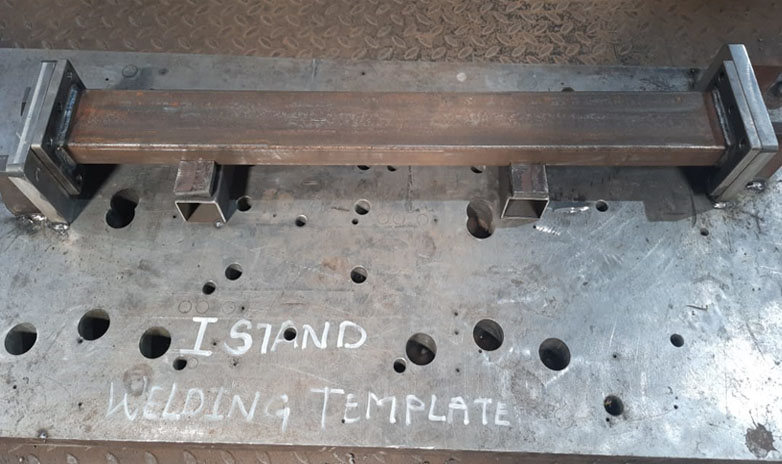
SOLUTION FOR ANGULAR TUBE WELD
Problem 2
Difficulties were found to hold the two tubular or angular pipes during welding in differ angles.
Advent Solution
- We started to use standard Magnetic Angular blocks which is easily available in market to hold the tubes during welding .
- Magnetic block can easily hold and guide the Tubes or pipes in required angle for weld.
- We can hold tubes or pipe which has to be weld in different angles like in Right angle 75°, 45°, 60°, 30°etc.
- By using this Angular Magnetic blocks welding process becomes easy & it is done properly without any distortions.
Benefits
- Tubular pipes can easily hold and weld.
- It is time saving & reduce extra man power for holding the two pipes or tubes during welding.
- Reduced bending or angle issue after weld.
- Welding tubes or pipes can easily hold in required differ angles.
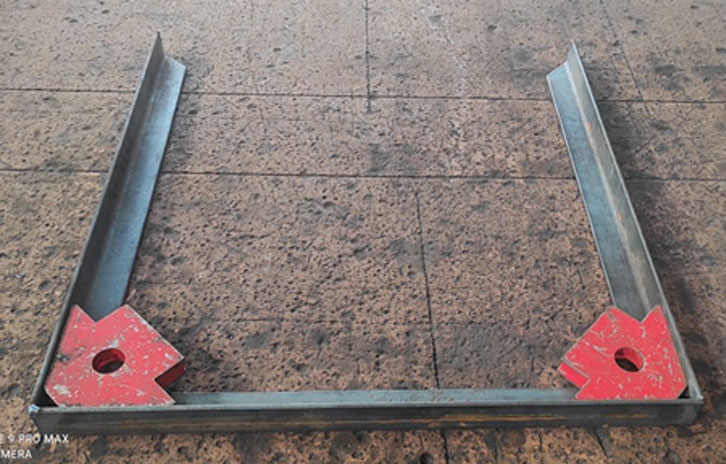
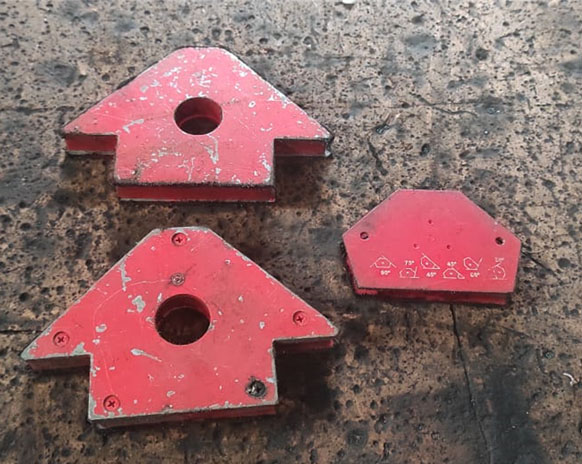
SOLUTION FOR WELDING OF AUTOMOBILES PARTS ASSEMBLIES
Problem 3
Difficulties were found during Welding Automobile parts assemblies. Which is complicated to weld.
Advent Solution
- Advent manufactured the welding fixtures for locate the child parts with location pins, to support child parts mounting and holding the work piece by heavy clamps, in required position to obtain a precise product from a process.
- A welding fixture is designed in a way to support and locate the components to be welded to avoid distortions and weld stresses.
Benefits
- With the help of welding fixtures & weld templates it is easily accessible to the point of weld.
- Work pieces easily fixed & removed before & after Assembly.
- Part can easily hold in most convenient position for welding.
- Provided suitable clamping to avoid distortion in weld.
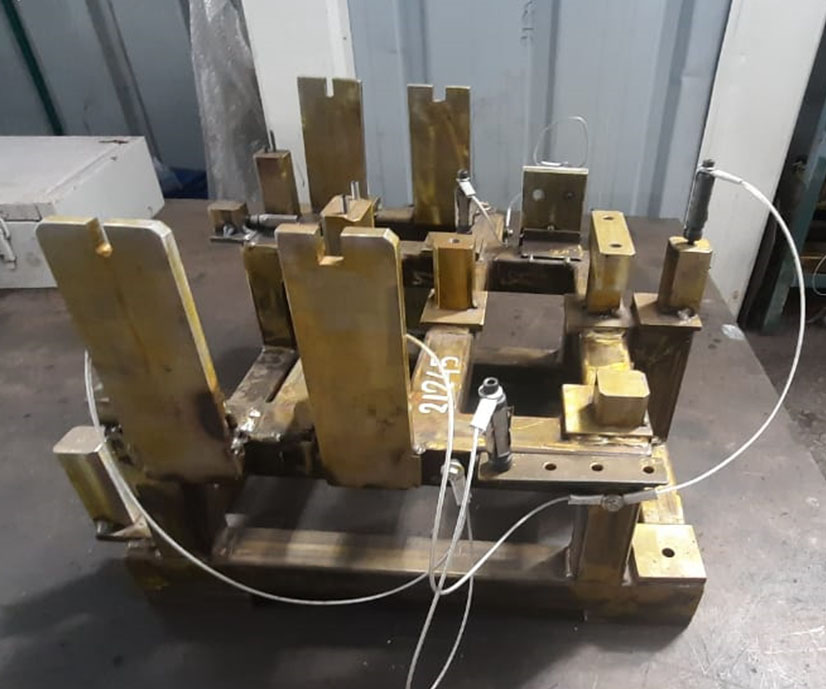
Leave a Reply